Best Industrial O-Rings Manufacturer

Importance of O-Rings
In the world of engineering and manufacturing, it’s often the smallest components that play the most critical roles. Among these unsung heroes is the unassuming yet remarkably versatile O-ring. These small, circular seals may seem insignificant at first glance, but their impact and importance extend across a wide range of industries and applications. In this article, we will delve into the world of O-rings, exploring their design, functions, materials, and diverse applications that make them indispensable in modern technology.
An O-ring is a doughnut-shaped gasket designed to seal gaps between two or more parts. It is typically made from elastomers, which are flexible and resilient materials that allow the O-ring to deform under pressure and return to its original shape when the pressure is released. This unique design gives O-rings their sealing capabilities across a wide range of environments and pressures.
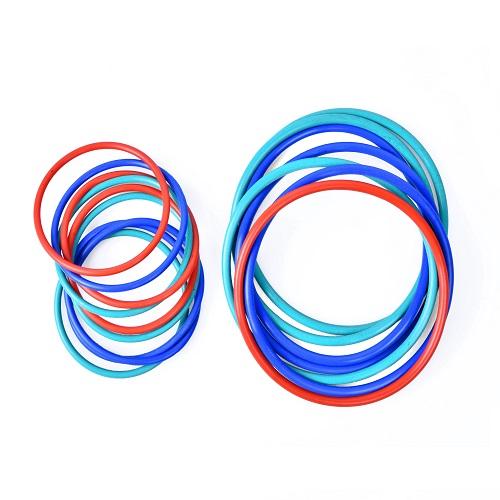
-
Sealing: The primary function of an O-ring is to create a reliable and leak-free seal between two mating surfaces. Whether it’s preventing the escape of gases or fluids, O-rings ensure that vital systems remain operational and efficient.
-
Pressure and Vibration Resistance: O-rings are capable of withstanding both static and dynamic pressures, making them ideal for applications that involve vibrations, oscillations, or sudden pressure changes.
-
Temperature Range: O-rings can handle a wide range of temperatures, from extremely cold to extremely hot environments, making them suitable for use in various industries, including aerospace, automotive, and industrial manufacturing.
-
Chemical Compatibility: Different elastomeric materials can be chosen for O-rings based on their compatibility with specific chemicals. This feature is crucial in industries where contact with various substances is common.
-
Rubber Bellows Supplier in Pune
Rubber Bellows Supplier in Pune Rubber Bellows Supplier in PuneIntroductionWhat is... -
How to Choose the Best Oil Seals Manufacturer: Why Shende Sales Corporation Stands Out
Introduction One of the top manufacturers of industrial oil seals and... -
Circlips Manufacturer in India
Circlips Manufacturer in India Circlips Manufacturer in IndiaIntroductionWhat Exactly Are CirclipsWhy... -
Rubber Bushes Manufacturer in Pune
Rubber Bushes Manufacturer in Pune Rubber Bushes Manufacturer in PuneIntroductionWhat are... -
Oil Seals Manufacturer in Pune
Oil Seals Manufacturer in Pune Oil Seals Manufacturer in PuneIntroductionWhat Exactly...
Materials Matter
The effectiveness of an O-ring greatly depends on the material chosen for its construction. Different applications call for specific materials that exhibit varying levels of resistance to temperature, pressure, and chemicals. Common O-ring materials include:
-
Nitrile (NBR): Known for its excellent oil resistance, nitrile O-rings are commonly used in automotive and industrial applications.
-
Viton (FKM): With exceptional chemical and heat resistance, Viton O-rings find a home in aerospace, chemical processing, and high-temperature applications.
-
Silicone (VMQ): Silicone O-rings are often used in food and medical industries due to their low toxicity and wide temperature range.
-
EPDM: EPDM O-rings excel in outdoor and water-related applications due to their excellent weather and water resistance.
-
PTFE (Teflon): PTFE O-rings possess outstanding chemical resistance and are frequently utilized in applications involving aggressive chemicals.
Diverse Applications
O-rings find their way into countless applications, contributing to the functionality and safety of numerous products and systems:
-
Automotive: O-rings are used in engines, transmissions, fuel systems, and air conditioning units to maintain reliable seals and prevent leaks.
-
Aerospace: In aircraft engines and hydraulic systems, O-rings ensure the integrity of critical components under extreme conditions.
-
Medical Devices: O-rings play a pivotal role in medical devices, such as syringes, pumps, and valves, where leak prevention and chemical compatibility are paramount.
-
Industrial Manufacturing: O-rings are used in hydraulic and pneumatic systems, pumps, valves, and compressors to ensure efficient operation and prevent fluid leakage.
-
Consumer Electronics: O-rings are used in waterproofing and sealing electronic devices, protecting them from moisture and environmental factors.